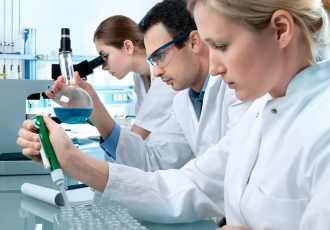
After production and calibration, all of the volumetric items must have a quality check to assure the accuracy of the calibration according to DIN (Deutsches Institut für Normung) standards.
By using deionized water, the gauge has to be filled exactly up to the mark, accurately hit the meniscus and put on a vessel to check the weight. Depending on various factors like water, room temperature, humidity and air pressure, the exact volume of water can be calculated from weight. The deviation between filled in volume and well defined mark should be at least ten times more accurate than the allowed error limits.
This manual process of the quality control is very complex and time consuming. Only a well experienced operator is able to make this control, even then the results might have a lack of reliability. In order to avoid these risks and achieve utmost accuracy together with reliable test results all the time, ISOLAB has implemented a fully automized quality control system.
Q.C.C® works with a high resolution CCD camera system and image processing in order to find the meniscus and adjust the filled volume. The balance and thermometer are in-line connected to the system. It has a closed loop deionized water system to ensure high precision among volumetric measuring instruments.
By eliminating the risk of human factor, Q.C.C® guarantees accuracy and constant quality of the products any time, independent from any external factor.