QUALITY CONTROL & CERTIFICATION
As one of the most important operation fields for ISOLAB, the biotech industry always requires certification for the plastics they use and market trends clearly indicate a need for DNase, RNase and pyrogen-free products. Moreover, well reputable pharmaceutical and diagnostics companies cannot accept their samples or products to be contaminated. Most of our products are IVD class items which need to be produced according to special conditions. Thus, as being a worldwide trusted plastic manufacturer; ISOLAB puts great emphasis on the quality and cleanness of its products as well as their certifications.
Certified plastics mean an ongoing quality control process, instead of a single test applied to the final product. The process begins with inspection of the raw materials to monitoring the final product and ends with testing each lot after production for contaminants.
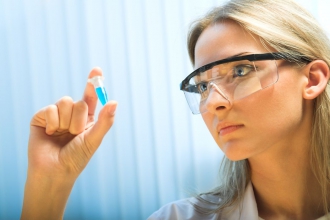
For sterile products, the initial microbiological tests are done for clean rooms. The production can start only if the conditions of the clean rooms are valid. Also every batch of products is controlled with “Tryptic Soy Agar” at the end of an incubation period of 48 hours at 35-37°C and with “Saboround Dextrose Agar” at the end of an incubation period of 5 days at 22-25°C. Only if these two controls pass the tests, then the products are taken outside the quarantine room. Hence every aseptically produced product has to be kept at least 5 days in warehouse before dispatch.
The growing fields of biotechnology and biomedical research such as gene therapy, molecular biology and DNA diagnostics, require a much more intense control of certified, contaminant-free, safe products. ISOLAB is proud to position itself as one of the few plastic manufacturers that completely fulfills all the requirements mentioned above and serves its wide variety of valuable customers in the best possible way.